SHOT BLASTING MACHINE
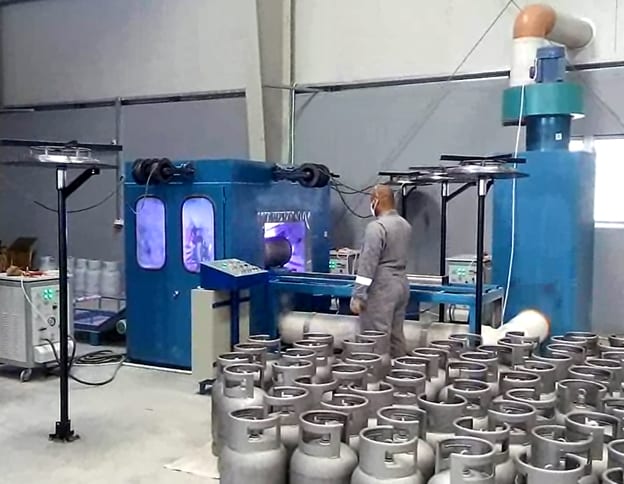
Automated LPG Cylinder Shot Blasting Machine
1. Machine description
Our shot blasting machine is especially made for gas cylinder. Using the high speed shot to hit the surface of the cylinder, so that to clean the oxide-scale and make the cylinder surface silver gray and remove the inner stress of the cylinder, improve the surface adhesive force. Meanwhile, we will increase the compressive pre-stress through shot blasting to improve rigidity.
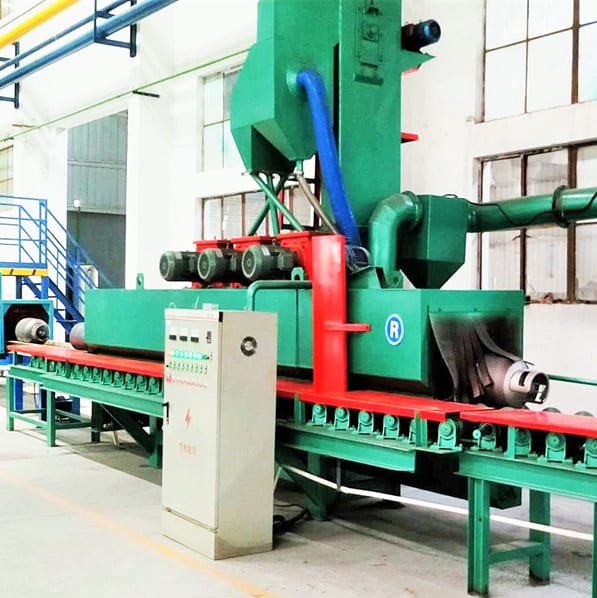
2. Main technical data
No | Name | Model | Unit | |
1 | Efficiency | 170 | pcs/h | |
2 | Workpiece | Weight | ||
Size | 33kg φ356×1055 | mm | ||
12.5kg φ302×570 | ||||
3 | Shot blasting machine | Quantity | 4 | set |
Model | Q034Z8I | |||
Sands consumption | 220 ´ 4 | kg/min | ||
Motor power | 15´ 4 | KW | ||
4 | Shot | Particle size | 0.5~0.8 | mm |
Material | Cast steel shot, wire shot | |||
Hardness | HRC45~55 | |||
First input | About 2000 | kg | ||
5 | Bucket hoister | Lifting capacity | 60 | t/h |
Bucket width | 215 | mm | ||
Bucket distance | 300 | mm | ||
Line speed | 1.25 | m/s | ||
Valid lifting distance | 7000 | mm | ||
Motor power | 5.5 | kw | ||
6 | Shot slag separator | Separator capacity | 60 | t/h |
Separator air volume | 1000 | m3/h | ||
Separator efficiency | >99.5% | |||
Valid separator width | 1000 | mm | ||
Rotation speed of rotary screen | 43 | r/min | ||
Motor | 3 | kw | ||
7 | Ventilation and dust removal system | Chamber air volume | 12000 | m3/h |
Separator air volume | 1000 | m3/h | ||
Total air volume | About 13000 | m3/h | ||
Dust removal type | (cyclone+filter drum) secondary dust remover | |||
Dust remover model | CLT240 | |||
Filter area | 240 | m2 | ||
Main fan power | 15 | kw | ||
8 | Spiral conveyor | Convey capacity | 60 | t/h |
Motor power | 3 | t/h | ||
9 | Machine total power | ~83.5 | kw |
3. Machine structure
The whole machine structure consists of shot blasting chamber(1 set), shot blasting machine(4 sets), hoister(1 set), separator(1 set), platform, ladder, railing(1 set), spiral conveyor(1 set), shot supply system(4 sets), electric control system(1 set), dust remover system(1 set), pneumatic control system.
- Shot blasting chamber and sealing protection system
Chamber structure and protection
Shot blasting chamber is welded by structural steel and steel sheet with enough strength and rigidity. There are wear-resisting cast iron protection plates everywhere in the shot blasting chamber to prevent the shot getting out of the chamber. There is also wear-resisting grating plate to prevent the shots hit the funnel.
Top groove sealing
To protect the hook and slider inside of the top of the chamber, we use protection plate and wear-resisting slab, nylon brush to create a labyrinth sealing tape(Switzerland+GF+our company technology). Making sure no spot will come out of the chamber.
- Shot blasting assembly
Shot blasting assembly consists of shot blasting machine and motor.
Shot blasting arrangement:
This machine has totally four shot blasting machine, the arrangement of angle and position is designed by computer dynamic simulation, then confirm. Trying the best to avoid empty shot to increase the shot utilization rate.
Shot blasting machine:
Our direct-connected shot blasting machine combine the technology features of English SPENCER and American WHEELBRATER. Shot blasting machine consists of impeller and impeller driving plate, orientation sleeve, motor, cover piece, high chrome wear-resisting protection plate, slab, shot feeding tube, bottom plate and so on.
The impeller directly connect with the driving motor, so that avoid spares – transfer belt. Also it takes small occupied area, can be suitable with the shot blasting position.
Features of the shot blasting machine:
- High efficiency: reduce about 10%-15% energy consumption, the shot blasting capacity is up to 16~20kg/min·kW.
- Valid sealing: use protection plate and wear-resisting slab, nylon brush to create a labyrinth sealing tape (Switzerland+GF+our company technology). Making sure no spot will come out of the chamber.
- Quick dis-assembly of the blade: do not need any other tooling, dis-assembly 8 blades only need 5-10 minutes. Since the blades are fixed by the impeller’s rotation centrifugal force, so you need to take out the orientation sleeve and impeller before dis-assembly the blades.
- Adopt double-disc impeller, very stable, the shot area is concentrated and uniform.
- The blades and impeller and orientation sleeve are high chrome wear-resisting material. The blade weight tolerance<5g, largely lower the noise(<85db).
- Beautiful appearance and structure.
- The inhibiting device is installed on the shot blasting. When we open the top of the shot blasting machine, it ensures the machine will not start to keep people safe.nn
- The whole shot blasting noise depends on shot blasting machine. We also can customize the sound proof box on the machine, also we can directly shield the whole machine.
- Shot slag separator
Description:
Our separator is the most advanced technology in the world, the separator efficiency ≥99.5%, adopts technology from Swiss GEORGE FISCHER DISA(GIFA) and American Pangborn. The separator is the key parts of the shot blasting machine, the size of separating area will directly affect the separating.
Components of the separator: rotary screen and winnowing system.
Working principle of the separator
The shot slag mixtures will be lifted into the rotary screen by hoister. Outside the rotary screen are the spiral blades, which will discharge large pieces of debris through slag-drip hole. Then the shots, gravels and dust will be spread evenly along the separator, equally pressure on the balance plate. If the shot pressure to the balance plate against torque risen from cutter point < cutter point torque from balance plate, the balance plate will be closed. If the shot pressure to the balance plate against torque risen from cutter point = cutter point torque from balance plate, the balance plate will be free and shots will fall as a think curtain. Because the hopper opening area on the balance plate is fixed, the shot pressure on the balance plate against cutter point torque is fixed also. Only needing to adjust the position of balance weight, it can separate in high quality.
During the process of falling below, the shots slag mixture will do curvilinear motion, driven by horizontal air flow. Due to the difference of the weight and size of the shot and slag, their deflection is different, then they will separated. The dust will be inhaled into the dust remover, broken shot and slag and scale cinder will enter the trash tank, finally the qualified shot will enter the storage hopper and be recycling used.
Range of the separator: To ensure the best separating, the shot diameter is f1.2~f3.0mm, the separating efficiency is ≥ 99.5%.
- Bucket hoister
Principle and constitution of the bucket hoister: the machine is driven by flat belt, will unload the material through centrifugal gravity. The hoister consists of cycloidal reducer, upper and bottom roller, tape conveyor, hopper, closed material cylinder, tension device. The feeding hole is connected with spiral conveyor, and the discharge hole is connected with the separator.
Function and structure
The cover of the hoister is bending formed and welded. There is access door on the cover, which is convenient for changing the material hopper in time. When you open the door on the bottom cover, you can repair the bottom driving device and eliminate the obstruction of the shots. When it is working, the hopper on the tape conveyor will lifted up the shots to the top driven by the motor. Lastly, the shot will enter the separator. To ensure the tape conveyor will not slip during the working process, the roller is like squirrel cage, which enhance the friction between the tape and belt wheel, also prolong the service life. When the belt is slack, we can tighten the belt through the tension device. The pulse wheel is installed on the bottom spindle of the hoister, which can monitoring the working condition. When problems occurred, PLC will get this signal and keep the safe of the machine.
- Spiral conveyor
Function of the spiral conveyor: It will be directly installed on the hopper at the bottom of the chamber. The exit of the conveyor is connected with the hoister. Spiral blades will mix all scattered shot slag mixture on the bucket hoister.
Constitution of the spiral conveyor: cycloidal reducer, screw spindle, conveyor cover, mounted bearings. That is a standard horizontal shot conveyor, and is the main part of the shot recycling system.
The spiral blades is 16Mn. The inner and outer circle is drawing by special technics with accurate pitch and size. Can be use for a long time.
4. Electrical specification
- Working condition
Power: three phase four wire, alternating current 380V, 33Z
Environment temperature: 0ºC~+55ºC
Environment humidity:35~45%(non-condensate)
- Summarize
The electric system is operated manually, showing the working state and part fault diagnosis function. It has shot blasting cycle timer, can accumulate the working time and how it. The system is very safe with interlocking and self-locking function and emergency stop button.
5. Inspection standard
Shot blasting machine: impeller body radial run-out≤0.15mm, face run-out≤0.05mm, dynamic balance detection ≤ 18 N.mm, blank running the main spindle for one hour, the temperature will increase ≤ 35ºC.Separator: After separator, in the qualified shots, slag ≤ 1%, in the dust and other dun-dries, qualified shot ≤ 0.5%.
6. Supply range
No | Name | Qty | Remark |
1 | Cleaning room | 1 | Wear-resisting cast steel plate |
2 | Shot blasting assembly 2 | 2 | American WHEELERB RATOR technology Protection plate is high chrome cast steel, Cr≥18% |
3 | Shot blasting assembly 2 | 2 | |
4 | Electric system | 1 | Normal control |
5 | Bucket hoister | 1 | Cycloidal reducer |
6 | Spiral conveyor | 1 | Cycloidal reducer |
7 | Shot slag separator | 1 | American PANBRON technology with cycloidal reducer |
8 | Shot control system | 4 | Imported Airtac air cylinder |
9 | Chamber | 1 | Wear-resisting rubber protection plate |
10 | Pneumatic system | 1 | Imported Airtac pneumatic components, air source system, air cylinder |
11 | Dust remover | 1 | Cyclone dust remover, impulse filter dust remover, fan, tube, chimney |
12 | Platform,ladder, rail | 1 |
7. Carried spares
Name | Model | Quantity | Note |
Impeller | Q034Z8-3 | 4 | |
Orientation sleeve | Q034Z8-2 | 4 | |
Blade | Q034Z8-1 | 32 |
8. Diagram
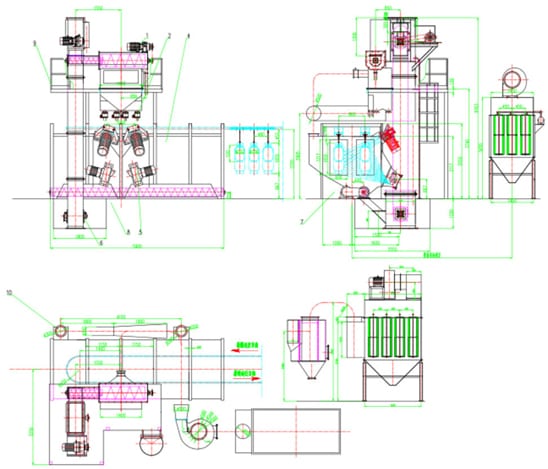
FAQ
LPG Cylinder Manufacturing Equipment
Q: What size of LPG cylinder your machine can produce?
A: 6kg, 12kg,15kgs and 50kgs LPG cylinder for cooking and other size according customers’ requirement.
Q: Can you design machines according LPG cylinder technical drawing?
A: Sure, please send your technical drawing to us.
Q: What are the benefits to choose your machines?
A: Our machines are strong and reliable for long term industrial manufacturing
To enable me give you correct proposal for correct machines, please tell me following details: We need to know following information to quote you correct machineries:
- Technical Drawing of the cylinders you want to make?
- What size of cylinder you want to produce? (6kg, 12kg)
- What diameter and thickness of the cylinder you want to make?
- Are you new in this area or you already have some machines in the workshop?
- Capacity you require, i.e. how many pieces and sizes you want to make per day?